DCS Group Dispatcher WMS Case Study
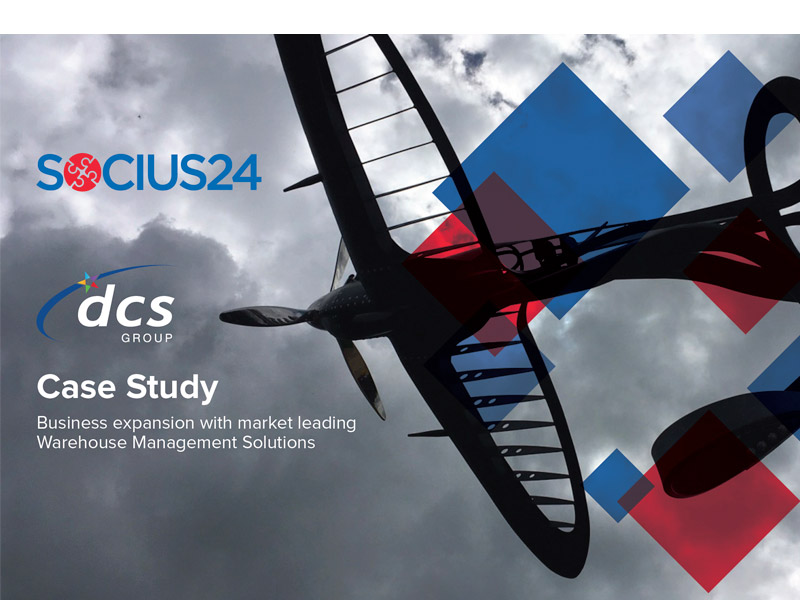
About DCS Group
The DCS Group was founded in 1994 by the current Chairman Denys Shortt OBE. The business opened its first commercial premises in Stratford-upon-Avon in 2001 before adding a manufacturing plant in 2005. Growing from three people in a stable block to a team of 400 people, with over two decades of selling health, beauty and household brands, DCS Group have generated £2 billion of sales. The company prides itself on driving growth for its customers, delivering value and loyalty.
Background
Whilst operations continue at Stratford-upon-Avon, the company outgrew this 11-acre site and opened a new facility in Banbury in 2017. The expansion into Banbury not only symbolised the success the company had achieved but also supported its expansion into new lines of business including Pharma.
The DCS Group has made a significant investment in the new Banbury site. The new facility features a huge lorry parking area for 26 trucks and trailers and a new 6 fast-tracking loading bay allowing the DCS Group to handle an increased amount of volume for their clients.
A powerful WMS needed to support growth and manage compliance
With the opening of the new 200,000 sq/ft distribution center in Banbury, DCS Group needed a new and sophisticated Warehouse Management System (WMS) that would enable effective management of stock across both the new site and the existing Warwickshire premises, with full integration to the company’s ERP system. It was also critical that the new WMS could handle the increased level of order volume the company would now be operating with, including a new pharmaceutical division. Key capabilities which needed to be delivered by the WMS included:
FEFO Methodology
Being able to manage a FEFO stock rotation methodology was also particularly important in relation to product expiry dates being accommodated for.
Traceability
All products must be accompanied by a unique barcode number for traceability purposes. DCS Group needed a system that could keep such specific information about every individual product but also have this readily accessible at any one time, even after the product had left the premises.
Compliance – Good Distribution Practices
Ensuring product quality is maintained throughout the duration of the distribution process is essential. In addition to this, being able to trace and provide an audit of a products’ full 360˚ journey, including; specifically what happened to the item, who has been responsible for it and at what point and what equipment has been used in relation to the product.
Solutions Delivered
The DCS Group selected Blue Yonder WMS, implementing the system at their Banbury site. Blue Yonder WMS scored higher than any alternative solution on DCS Group’s functional requirements grid and in particular, it was able to support the company’s scale and bespoke requirements.
Socius24 was chosen based on their deep understanding of the Blue Yonder WMS solution and also because of their extensive experience of warehouse operations. The entire project from project management and training to installation was provided by Socius24, including after-service support.
Outcome
Blue Yonder WMS and Socius24’s User Services Portal now run the entire warehouse operation at DCS Group, Banbury. Since the implementation, DCS Group has seen:
Improved Productivity
DCS Group are now able to accommodate a throughput of product with greater scalability–with the system managing full end to end processes.
Increased Access to Information
Managing everything through one system has resulted in bespoke reporting and analysis, making it easier for Warehouse Managers to have full control of their operations.
Traceability
All products are uniquely identifiable with barcode numbers and therefore can be easily tracked from receipt to dispatch.
Compliance
Audit trails are now readily available, allowing all areas of the business to have full visibility of each product’s journey through the warehouse.
Real-Time Information
Real-time alerts allow Managers and Warehouse Operatives to monitor their key processes and intervene before performance thresholds are breached.
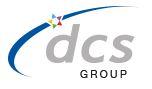