Conquering e-Commerce with Dispatcher WMS – Part Three
Conquering E-Commerce with Dispatcher WMS – Part Three
In the first article of this series, we looked at how doing receipts the right way can help you win at e-commerce. And then in the second article, we looked at how configuring your advanced WMS properly, so that it can make good decisions about what to do with those receipts. And we looked at how doing so can set you up for success later on in the warehousing process

So, in this third article, we’re going to assume that you’ve received your inventory and then it’s been directed by the system to an appropriate next step. Which means that today, we’re going to talk a bit more about moving inventory around your warehouse, and why you might want to do that.
If you’d like a quick overview of what we’re going to cover, watch this:
At its most simple, a warehouse management system needs to allow you to accurately receive inventory that you either know about in advance (pre-advised) or that just turns up on the receipt dock (blind receiving).

Then that WMS ideally will offer you an appropriate place to put that inventory away, dependent on how you’ve configured your system. And it’ll give you the opportunity to change the putaway location it suggested, and then, when you’ve put your stock somewhere, it’ll give you the opportunity to tell it where, how much and any other pertinent information.
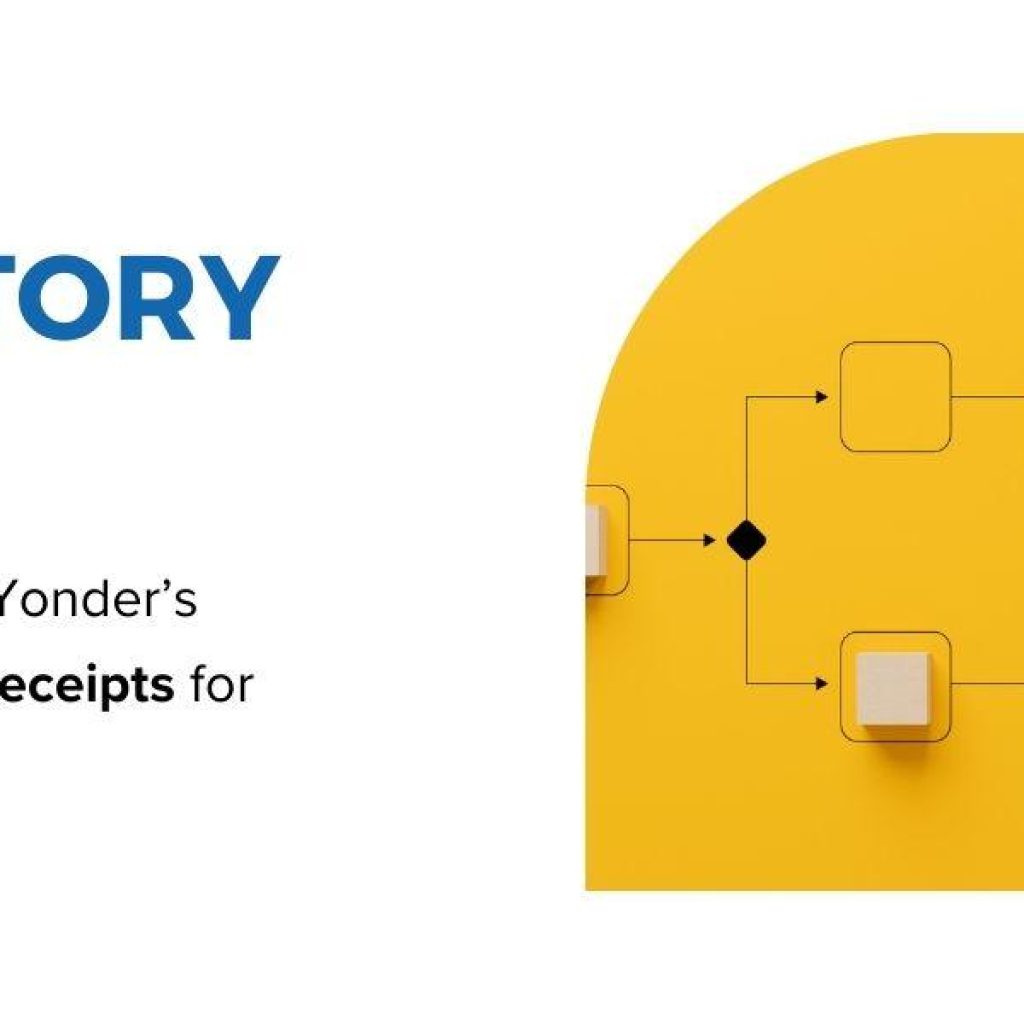
Then, when an order comes in, this simple model of a WMS will then be able to tell you what you’ve got on hand, where, and then allow you to go, remove what you need from that location, updating the information as it goes. And it’ll eventually allow you to remove it from your on hand records once it’s been shipped.
Working with a more advanced WMS, like Dispatcher WMS, can offer you a whole new world of efficiency and efficacy when it comes to moving your inventory around your warehouse. So, let’s have a look at what that could look like.
So, let’s imagine you’ve just received a SKU. As mentioned in the previous article, the first thing that your e-commerce Dispatcher WMS should do is to work out what’s the most efficient action to take with it. That may be putting it away, or it may be cross-docking it, or it may be creating a new pick face close to the ship docks for it (because it’s been identified by the system as a fast-moving SKU that your pickers will need easy and quick access to) and sending it there.
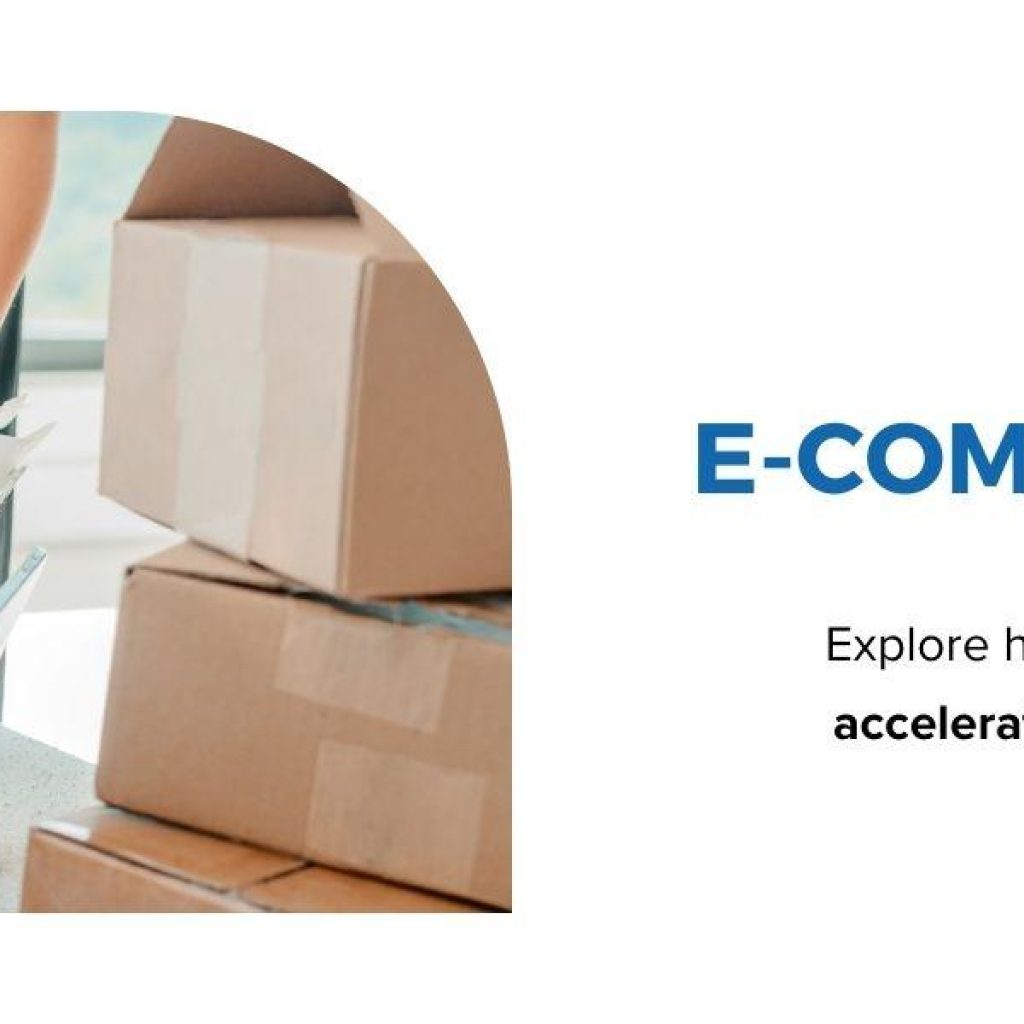
We talked previously about identifying receipts (typically returns) that need to be QA assessed, and how the system should deal with those. But that’s not the only option that your system has for QA. Even if you’re receiving non-returned inventory, you can set your system up to sample what you’ve just received. Perhaps you have a supplier that you need to keep an eye on. Perhaps the product is super expensive and you want to me doubly sure that you’re getting top quality merch. Perhaps it’s just that it’s easily broken in transit. Whatever reason you have to keep a close eye on certain SKUs (and in our experience, there are many), you have the option to automatically sample inventory (at a frequency, or under other conditions defined by you) upon receipt.
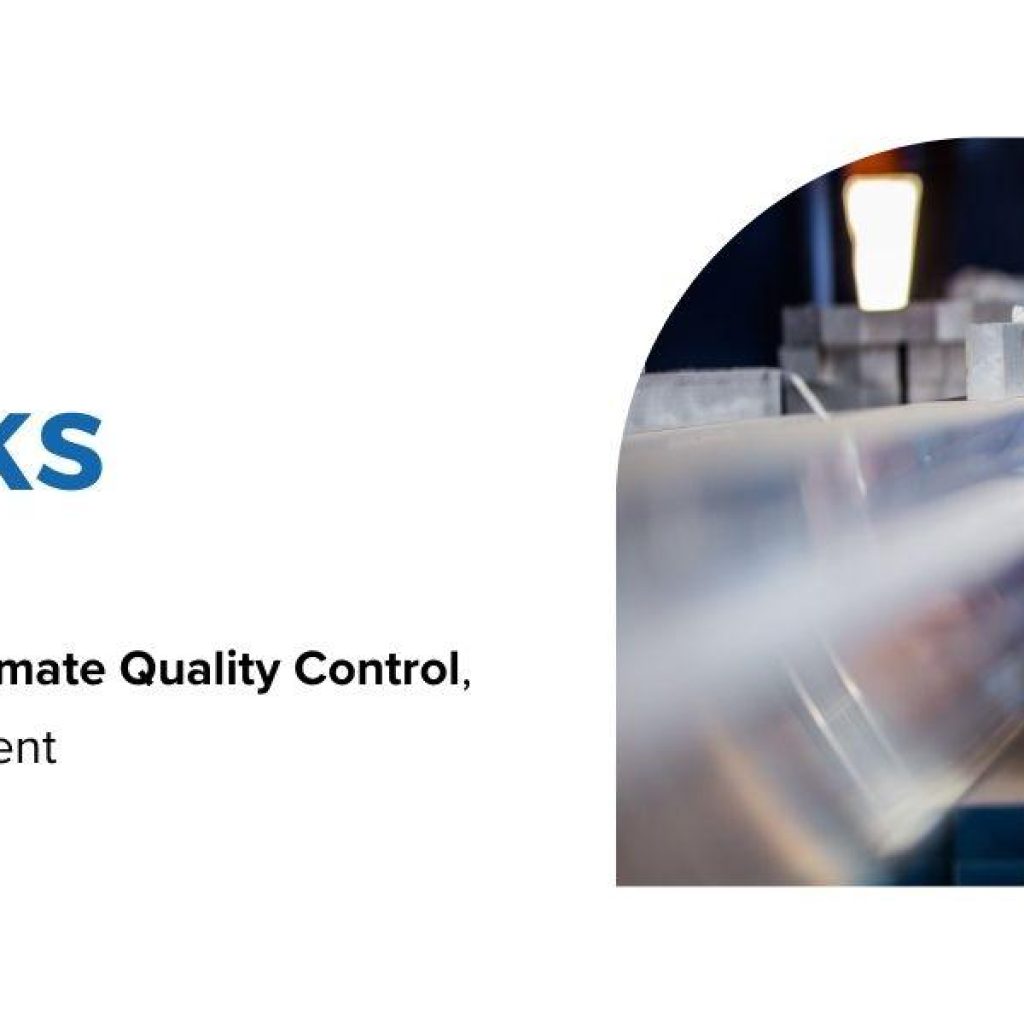
But say you’ve received it and your operator is putting it away. And then, as they handle it, they realise there’s a problem, whatever that problem may be. With an advanced WMS, your operator can submit it for QA in multiple different ways, and then, depending on how you’ve set up your system, it might be sent directly to your quality control area. Or it might just be put away where you were going to put it away, but with a lock code on it, so that it won’t be accidentally picked and shipped before someone checks it over. It’s up to you. You tell the system how you want it work, and that’s what it does.
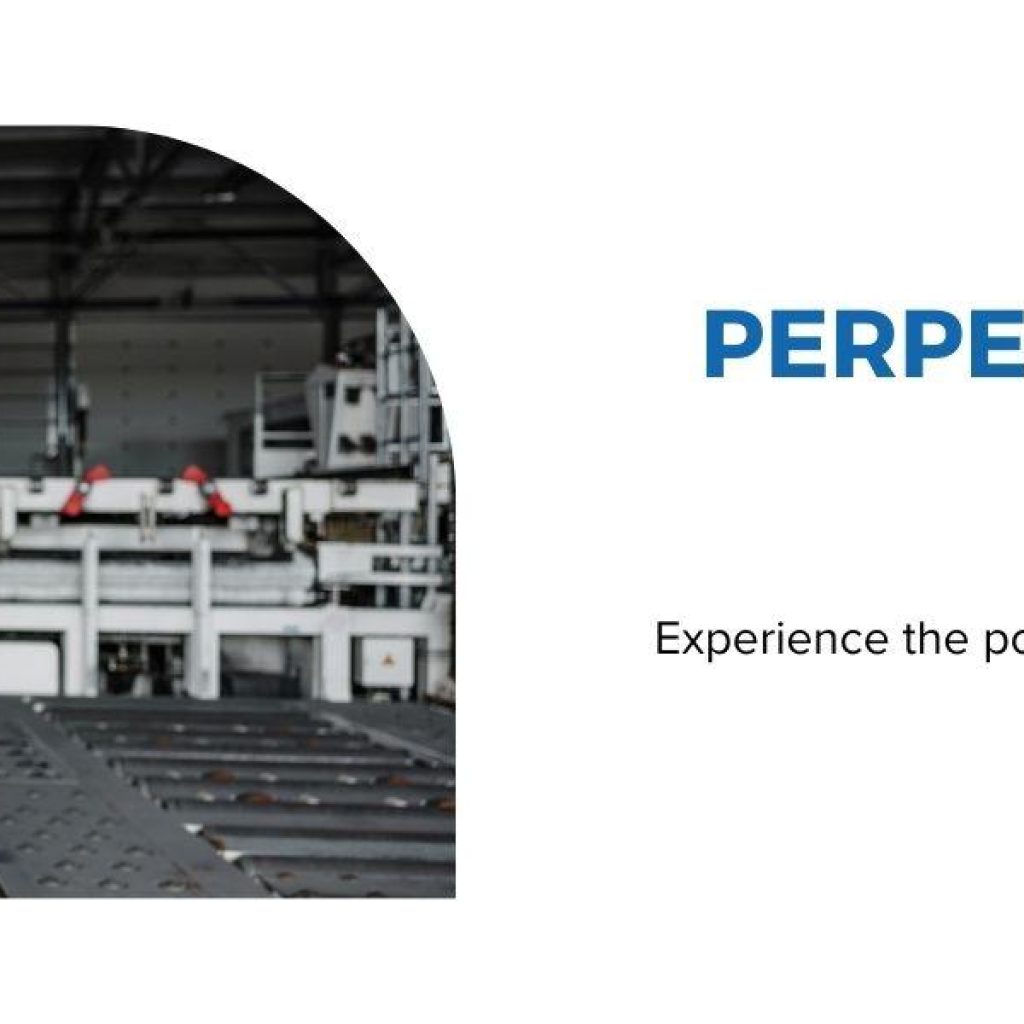
Or maybe, when they’re putting it away, your operator realises that there’s too much or not enough – there’s some kind of quantity mismatch. They can update the quantity there and then, and move on with their day. Or perhaps it’s not the batch that they were expecting… whatever it is, you can set up your system to run checks on that inventory every time it’s handled, and if your operators tell it something different to what it expects, it’ll make a note, and potentially change the next suggested step. In real-time. And then you can run reports either automatically or when you want to know what’s going on.
This is what Perpetual Inventory means – constant checking, constant monitoring, constant updating so that you can have near 100% accuracy too.
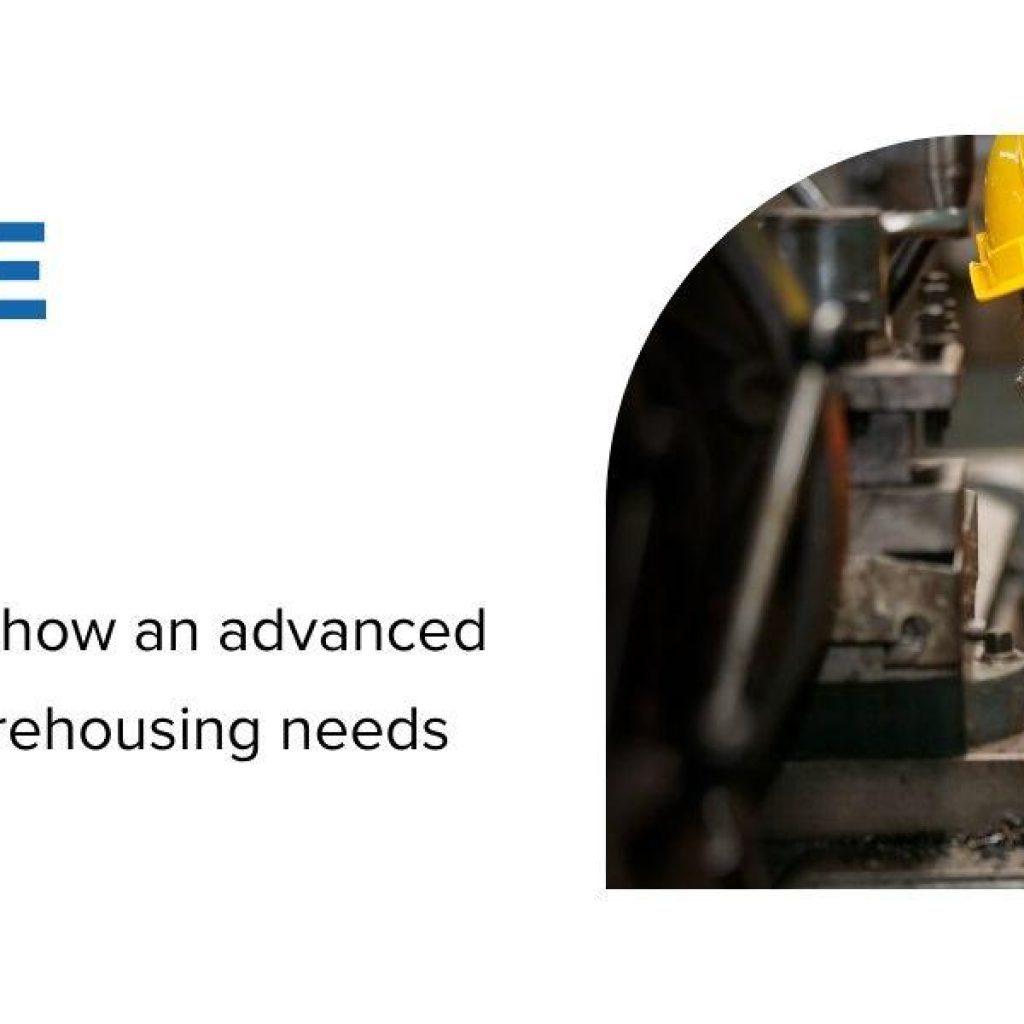
Other things that you might want to do to your inventory – Kitting and De-kitting. Perhaps you receive component parts, and you want to group them together before you ship them as a different product. Perhaps you receive an item, and you want to take it to pieces instead. Perhaps you’ll ship those parts individually, or perhaps you’ll use them some other way. Whatever reason you have for doing things like this, you can do them with an advanced WMS. And it’ll do all the calculations (just so long as you’ve given it the info first) for you.
Or perhaps you need to use different kinds of MHE in different parts of your warehouse. You can set an advanced WMS up so that it knows to swap tasks from one workstation to another, and where it needs to do that.
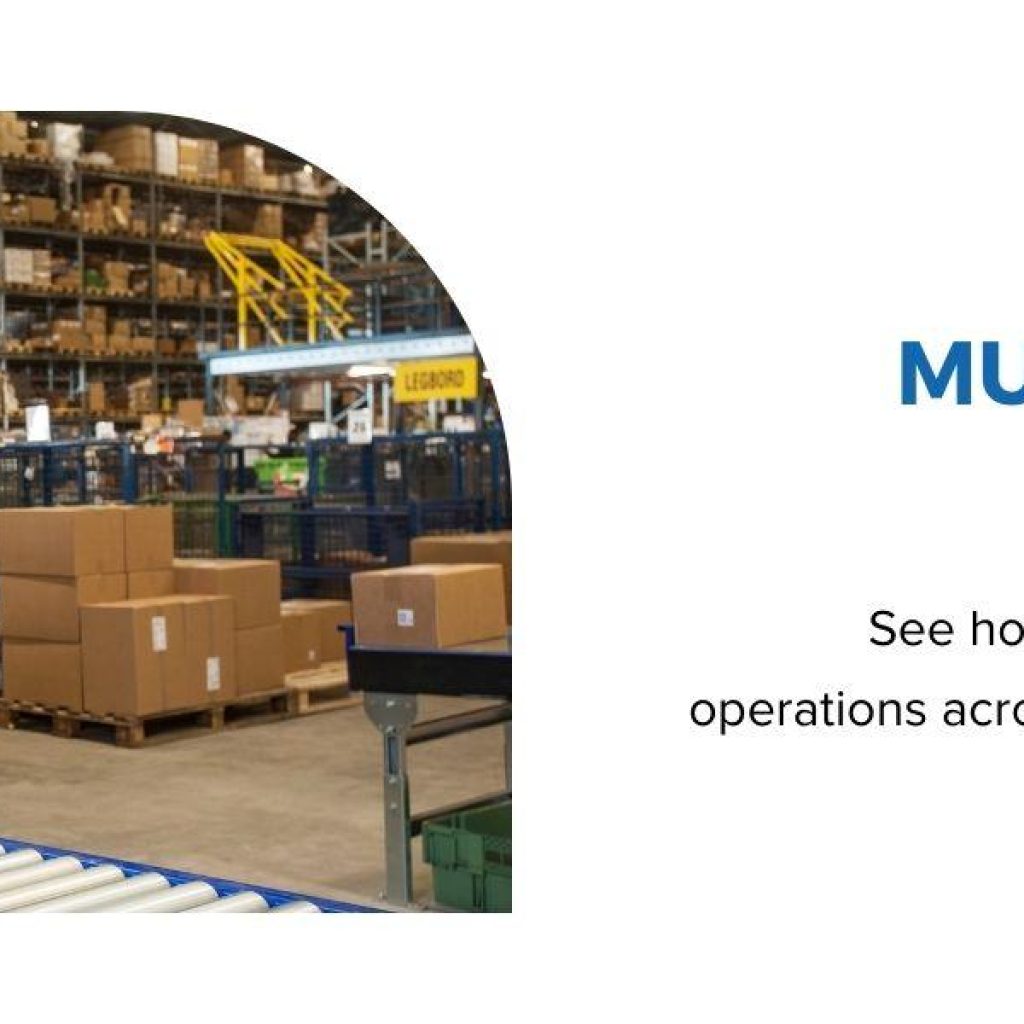
Maybe you have lots of warehouses on the same site, and it suits your purposes to start an order in one and then move it through the others, collecting order lines as it goes, until it reaches the ship dock of the final warehouse, which is where you’re going to load it onto the trailer.
There are as many different ways of handling inventory as there are people who do it. What’s important is that you find something that you can tailor to what you need to do NOW, and what will still be able to do what you need it to do as your business grows and your processes evolve.
In the final article of this series, we’re going to talk about what happens when you get an order, and how an advanced WMS can optimise you getting it out of the warehouse as quickly and efficiently as possible.
As ever, if you have questions, or want to talk about e-commerce uses of Dispatcher WMS (or User Services Portal, or eBilling – our mobile apps), you can always reach us on info@Socius24.com.
And if you’d like to read the final part of the series, click here.
If you’ve enjoyed this blog, claim your free subscription to our LinkedIn weekly Newsletter
– The World of WMS –
for more of the same great information!